Bakery and snack manufacturers need control of their recipes while ensuring high productivity levels. However, sometimes it can be difficult to evaluate the performance of one’s production line. Even when designed with yield and quality in mind, industrial kneading systems are subject to production hazards that impact their performance.
The measurement of key indicators can help to ensure the regularity of the production and identify action levers in case of productivity losses. Often misunderstood by companies, the OEE (Overall Equipment Effectiveness) is a revealing analysis tool of the performance, allowing comparisons on short or long periods of time as well as comparison between the production lines.
Why mesure the OEE?
Definition
The OEE measures the ratio between the time used for production and the time used by equipment. In other words, it seeks to calculate the amount of time the machine is used over the total time the machine has been available. The OEE should not be confused with the OOE (Overall Operations Effectiveness). The latter, unlike OEE, considers planned downtimes such as preventive maintenance, testing, breaks, and equipment load. It can therefore help complete the analysis but is not reliable to initiate the accurate ration of time used.
Benefits
The OEE is an easy to measure and reliable indicator, commonly used by many large companies. It integrates all the components of machine efficiency and engages different factors, both technical and human. It provides a global vision of production efficiency by considering all forms of productivity loss: breakdowns, defects, waiting times, and non-quality.
The three main goals of OEE:
- Improve the efficiency of resources and means of production
- Reduce waste of time and resources
- Optimization of productivity to improve the return on investment of equipment.
The positioning of the mixing equipment on the production line makes the calculation of the OEE particularly relevant. As it is positioned at the beginning of the line, the mixer’s performance will directly impact the performance of the whole production line. The line will never be able to produce more than the mixing equipment can deliver in terms of dough flow.
How to calculate the OEE?
The ideal value of the OEE to reach for any company is 100%. However, this is a theoretical value that will depend on the sector and the type of machine used. The primary purpose of the OEE is to drive continuous improvement. A high OEE means that the machine has been useful to production throughout the entire period of use. With optimal operation, equipment that is designed to run 24/7, such as continuous mixers, can achieve a very high rate of around 98%.
The constituents
Here is a diagram representing the different elements that constitute the OEE:
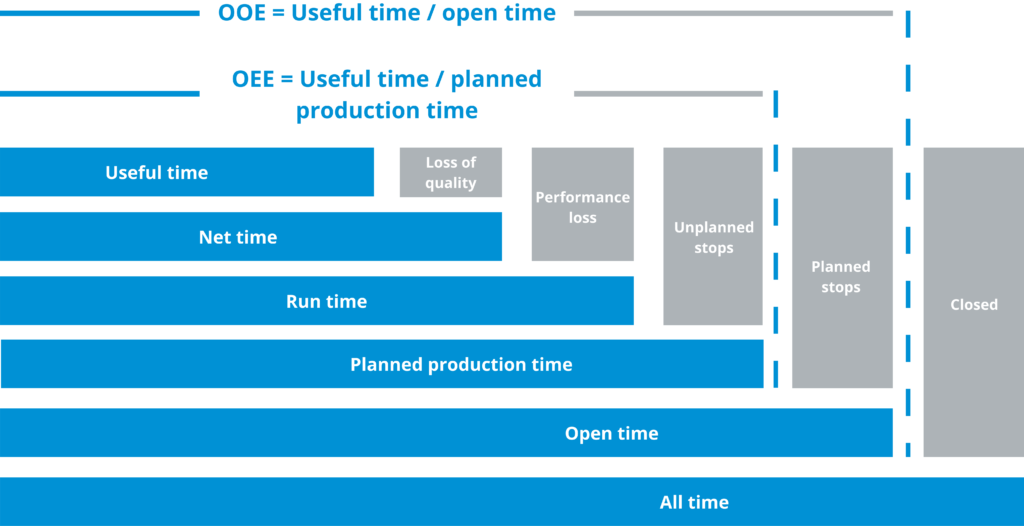
The OEE of a continuous mixer
Let’s take the example of the Verymix continuous mixer. It has a high kneading capacity, up to 8000kg/h. This type of equipment is designed to work in constant flow, and its OEE should close to 100%, however it is not always possible to reach this objective as many elements can interfere in the production process.
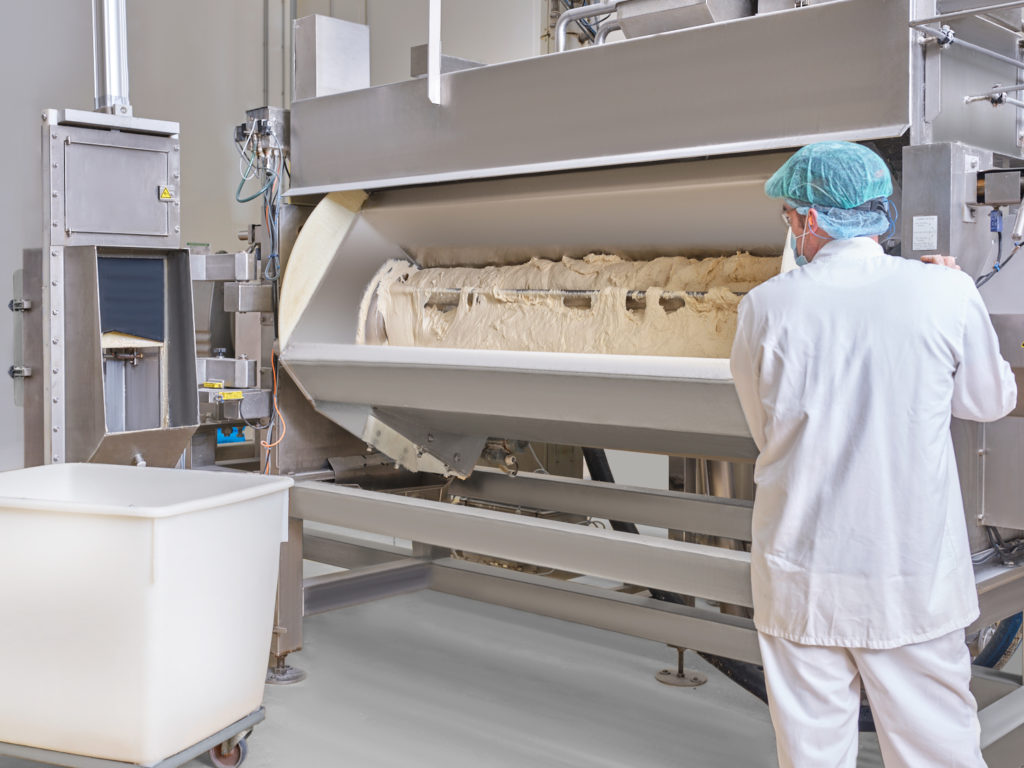
For a continuous mixer, several types of unplanned stops can be identified:
- Downtime due to operator’s intervention: operator suspension, operator filling
- Downtime due to the production cycle: line waiting, production changeover
- Machine failure: belt fault, guillotine fault, temperature fault, safety fault
These accumulated micro-stoppages can heavily affect productivity and the quality of the dough. Following a stop, the flow controls take up to one minute to restart. The system is blind (volumetric mode) during this time, and the flow controls are approximate which can contribute to issues in quality. Therefore, limiting downtime is a key issue in ensuring efficiency and consistency of production.
In a more detailed example, over six months (November-March), a continuous mixer in operation at a customer’s site had its lowest OEE in February, with 70%. Its average over the period was 81%. A detailed analysis of the equipment operation revealed a defect in the dough flow regulator at the tank outlet. The hours of non-production caused by this anomaly, associated with abnormally long line waiting times, considerably affected the OEE value and as a result, the line’s overall productivity over the month.
The regular measurement of the operating rate allowed the customer to have a reference and the ability to increase its OEE again in the following month to get closer to its average. The customer had the necessary information to take corrective action by displaying the defects and their duration. In this case, it was the intervention of a technician on the defective part of the machine (dough flow regulator). However, they still have option for additional improvement of their OEE to get closer to 100% by identifying the source of the line waiting times.
Elements to be considered to improve the OEE
In summary, to improve the OEE and, therefore, the productivity of your equipment, you must:
- Regularly analyze the results to easily identify the causes of various breakdowns and stops
- Effectively go back into the manufacturing process to identify the causes of non-conforming units
- Improve the organization to limit downtime due to human error
- Involve and motivate the whole team to ensure homogeneous management
- Identify the current situation and set objectives for the future
Which tools should you choose to monitor your production?
Monitoring the operation of your mixing equipment is essential to optimize its performance. Solutions exist at different levels to allow you to collect and analyze data related to your process.
- Solution 1: Control and supervision systems
Industrial equipment is equipped with comprehensive and intuitive HMIs to control the operation of the production line. The operator interface allows you to program and monitor your recipes, control the consumption of ingredients, the quantity of dough produced, or ensure the traceability of batches. A lot of information that is necessary to calculate the OEE is available from the HMI, such as the list of defects and their specific location. However, the functionalities of the interface at the foot of the machine remain limited. The data retention period cannot exceed a few weeks, and only the equipment data is displayed. With the supervision at the foot of the machine, it is therefore not possible to follow the evolution of the indicator over a significant period or to have a global view of the whole production.
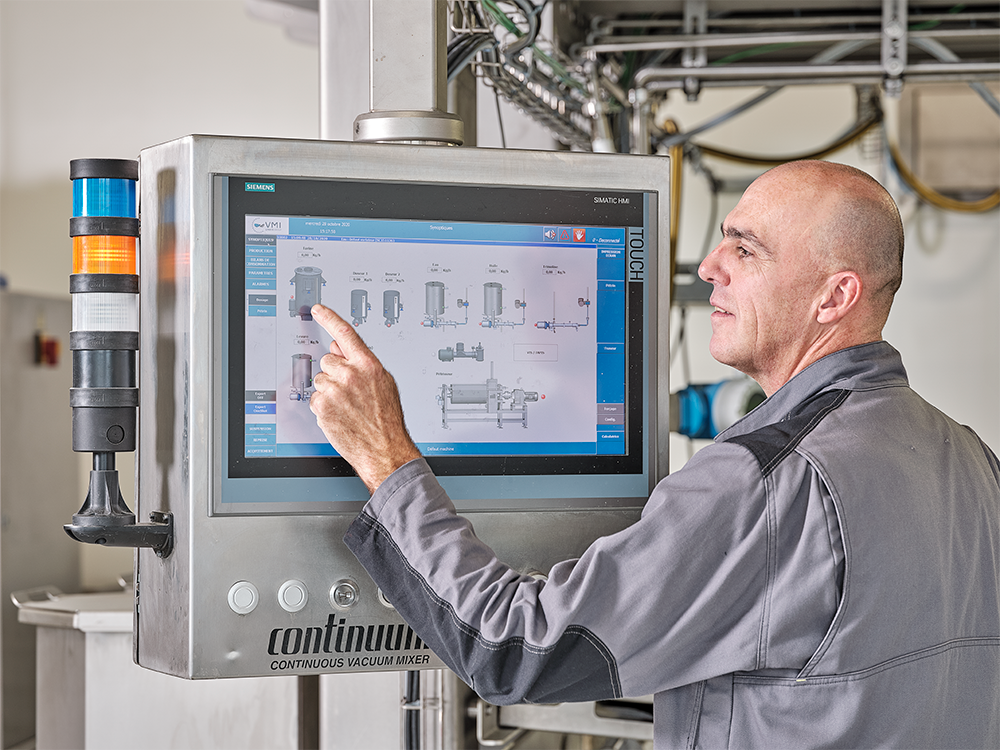
- Solution 2: Connected Business Intelligence
It is possible to connect your kneading and mixing equipment to the internet to collect, analyze, store and exploit data. Each piece of equipment is then equipped with technologies and sensors allowing data feedback. An interface displays this data in the form of information. The cross-referencing of numerous and complex data in the form of a visual and intuitive dashboard provides more relevant insight and, therefore, efficient decision-making. Using business intelligence with the IoT (Internet of Things) solution is undoubtedly the most effective solution for monitoring equipment operation rate, machine defects, and many other data related to its performance.
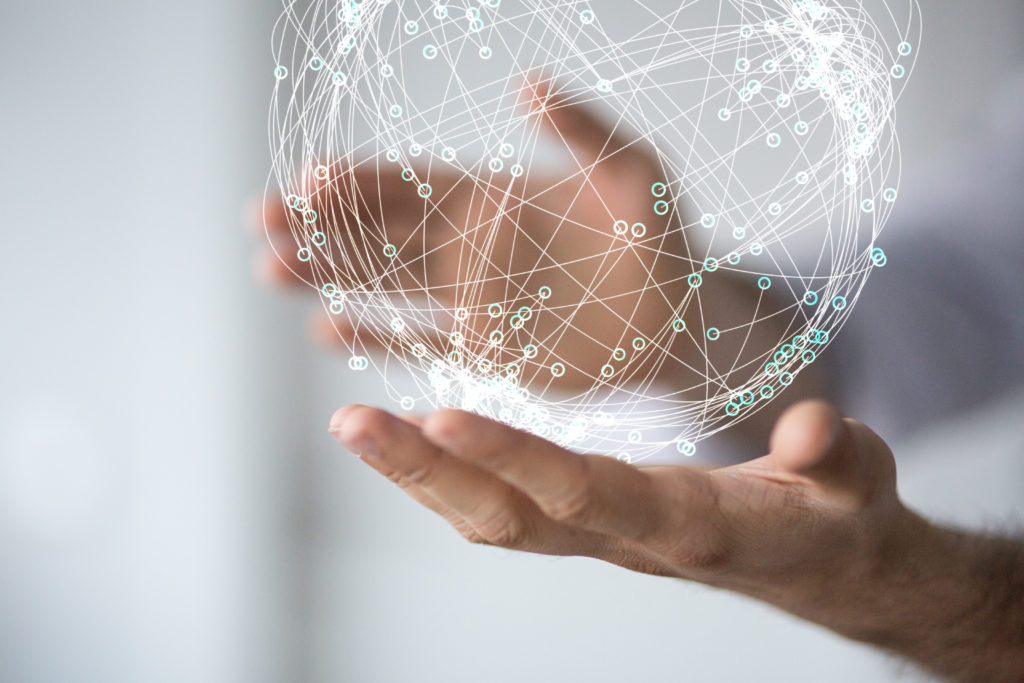
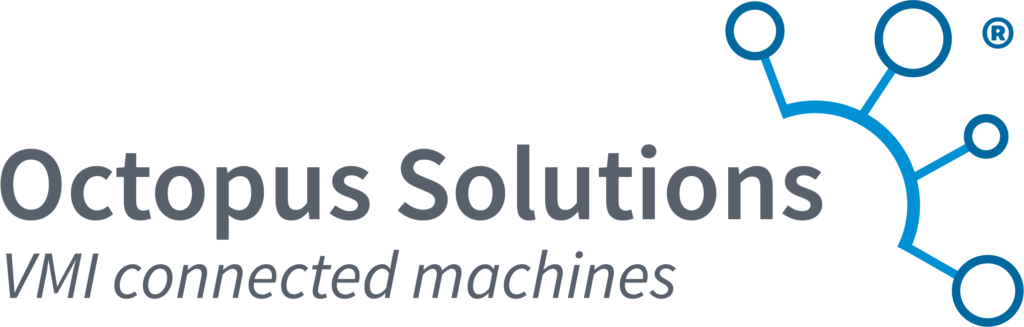
“Octopus Solutions” the IoT system developed by VMI, offers an intuitive and customizable interface to monitor the performance of your equipment. This tool gives you centralized control over your connected machines. You can visualize your operations, modulate the analysis periods and compare your different equipment. It is a very efficient tool to identify the causes of your lines’ stoppages and the specific location for quick correction.
How to implement corrective actions ?
Once you have identified the causes of downtime, you can make decisions to limit or even eliminate it. Solutions that can help you implement corrective actions:
- If human error is involved, proper training can avoid these stoppages. The follow-up and training of teams are essential to limit downtime or slowdowns. VMI offers a training catalog dedicated to mixing processes and equipment for all levels and professions and develops flexible training methods to meet the needs of bakery manufacturers.
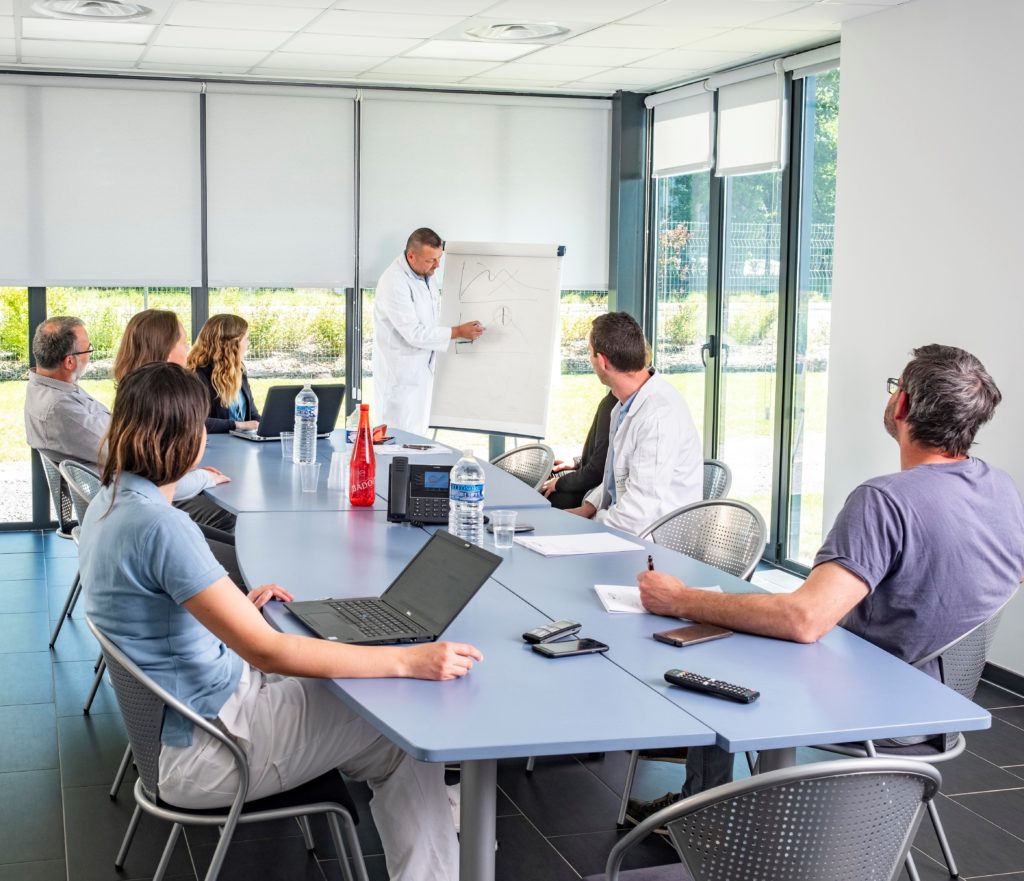
- Machine issue can signal that more regular and thorough maintenance may be recommended. Consistent maintenance visits are recommended for prevention before technical problems arise. Retrofitting operations can also help optimize the machine’s process or prevent equipment obsolescence.
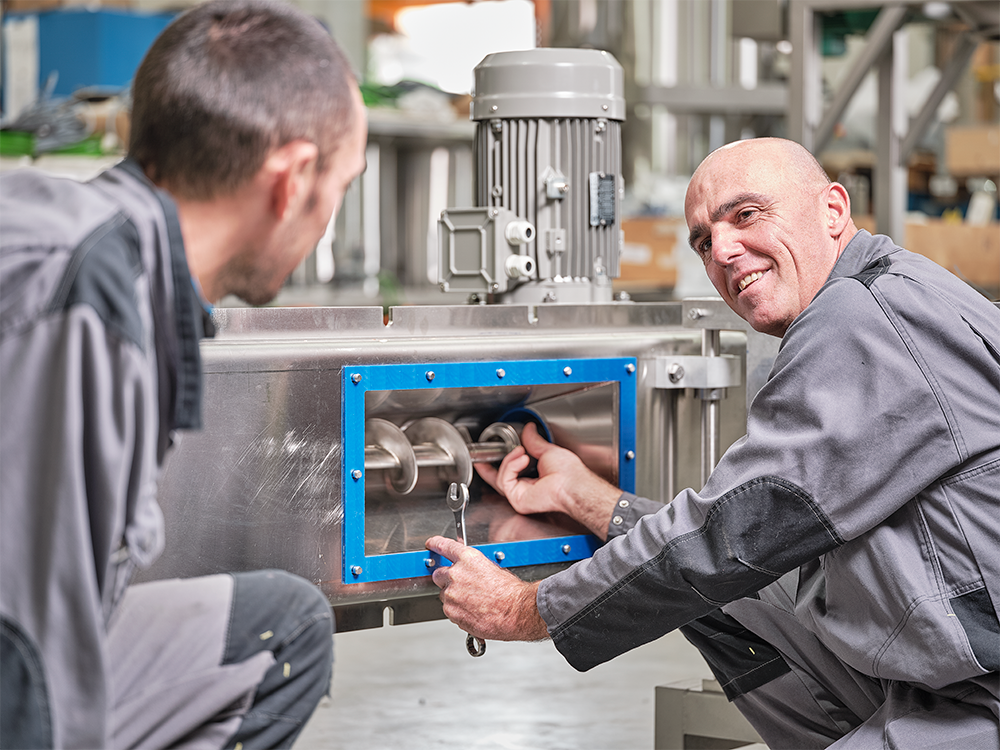
Therefore, the OEE is a crucial indicator for production managers in the bakery and snacking sector who want to monitor their performance daily while understand productivity losses. It highlights the points that need to be corrected and guides decision-making to improve the resources in place. This indicator is unifying because it involves the company on a global scale to implement a problem-solving approach. Improving the OEE of its mixing equipment ensures better productivity on its entire line for better profitability.