Any new product introduced on the market must first undergo strict controls to confirm its compliance with European Union rules and regulations. Does your bakery equipment meet the employer’s occupational health and safety obligations?
Purchasing bakery equipment: employer responsibility
Purchasing equipment engages the responsibility of companies towards their employees and communities. The consequences can be very serious in the event of failure to comply with European regulations. Therefore, this investment must include provisions to ensure employee safety.
There are different occupational hazards associated with the bakery profession. Among the most common are risks related to manual handling, falls, and repeated inhalation of flour dust. It is the employer’s responsibility to undertake to reduce the risk of occupational injury or illness, such as musculoskeletal disorders or baker’s asthma. In addition, it is critical to ensure that the equipment supplier is also committed to preventing these risks.
Does your new equipment comply with regulations? How can you ensure that it does and prevent your employees from being exposed to health and safety risks?
Here are a few things you should check when you invest in new equipment and before you put it into service:
Does my machine have all the required labeling?
A manufacturer’s label must be displayed on all equipment and must legibly feature the following information to identify the equipment and ensure accurate traceability:
- the name and address of the manufacturer, dealer, or importer
- the designation of the machine, its serial number, its year of construction
- the EC label
This information must be identical to that contained in the EC declaration of conformity and the instruction manual.
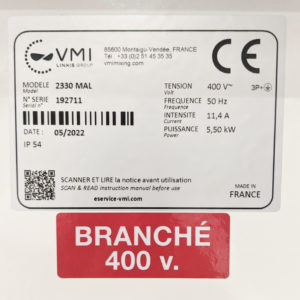
Have I been given the instruction manual and the declaration of conformity?
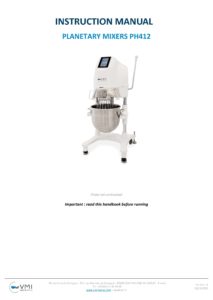
At the time of delivery, the seller must provide you with:
- a manual specifying the installation and operating conditions, and the machine’s operating restrictions.
It must also include information on emissions: noise, vibrations, radiation, and pollutants. - a declaration of conformity with the EC Machine Directive 2006/42/EC.
This declaration must be dated, signed, and include the manufacturer’s address.
Does the operation of my machine meet my expectations?
It may seem obvious, but don’t forget to check your machine upon receipt to ensure no damage occurred during transport. It must also function properly in all its intended operating modes.
Is the machine equipped with devices to prevent any related risks?
When a machine is used under normal operating conditions, safety rules require that the following operations be carried out without risk for the operator:
- transport
- installation
- setting up and adjustments
- standard operation
- maintenance and servicing
- disassembly
- disposal
It must be ensured that the manufacturer has taken all the appropriate measures to guarantee safe use throughout the equipment’s life cycle.
Prevention of mechanical risks
Access to zones presenting a danger for operators (mixing tools in movement, raising, and lowering of the head), must be prohibited or limited by setting up:
- fixed guards requiring a tool for their approval
- mobile guards: protective hood, safety fence when access to the zone is regular (the machine stops as soon as they are open)
- adjustable protective systems limiting access to the moving parts of the machines
- protective devices: light curtains, two-hand control
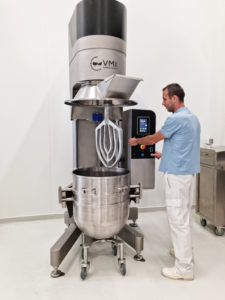
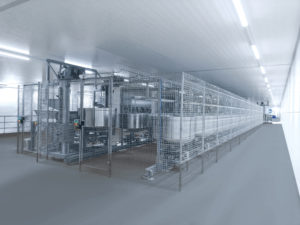
Appropriate labeling
All equipment and installations must be appropriately labeled. To ensure safe use, instructions must be clearly identifiable and easily understood: audible warning, light signal, pictograms, information in the user’s language, selector lockable by key or code, etc.
All machines must also have an operating device to ensure they can be safely started and stopped (push button, lever, pedal, switch, control handle, touch screen, etc.).
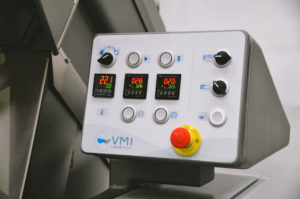
Is it safe to maintain my machine?
It is critical to ensure that your equipment’s adjustment and maintenance areas are easily accessible and located outside of hazardous areas. Maintenance operations must be performed by qualified and certified personnel with proper PPE and tools. You can find these guidelines in the instruction manual provided with your equipment.
Has the ergonomics of my equipment been assessed to ensure the health and comfort of the operator?
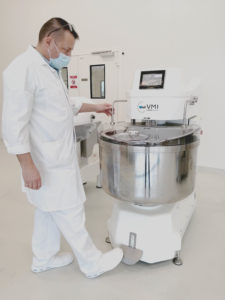
Choosing the appropriate equipment is very important because it can considerably impact the user’s daily life. Opting for an unsuitable machine or device can cause numerous physical and psychosocial problems. So before making a decision, ensure that every effort has been made to protect the user’s health, and in particular:
- limit excessive efforts
- avoid extreme joint positions
- reduce the handling of heavy loads
- reduce noise pollution
- facilitate work, cleaning, and maintenance operations
VMI commitments
VMI has been ISO 9001 certified since 1998 and has integrated a QSE/RSE policy into its management system to continuously improve the working conditions, safety, and health of its customers and employees.
Preventing the risk of accidents and improving workplace comfort and wellbeing are top priorities.
Our range of mixers, planetary mixers, and fermenters for bakeries is evolving to enable bakers to minimize awkward postures, manual handling, and flour dust emissions.
Would you like to know more about our ergonomic solutions?
Download the documentation now!
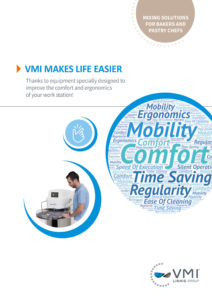