Whether you’re a professional in the pharmaceutical, cosmetics, or healthcare industry, investing in new production equipment—be it mixers, homogenizers, or other technologies—can be a significant challenge. How can you ensure that the equipment you choose will truly meet your specific needs?
Each application has its own requirements regarding performance, quality, cleanability, as well as traceability and compliance. But with the wide range of options available on the market, how can you make the right choice?
In this article, we will provide you with practical tips to define your needs and establish your specifications when purchasing production equipment, particularly a mixer. We will also discuss why conducting laboratory tests can be key to ensuring your project’s success.
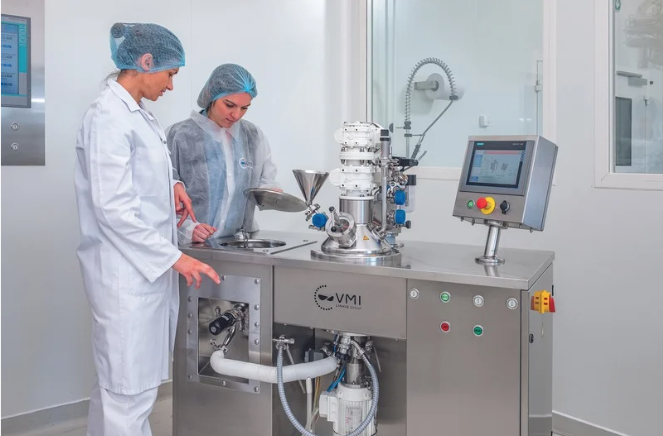
Step 1: Define your needs and establish detailed specifications
The first crucial step in planning any investment is to clearly define your needs through a detailed specification sheet. This document should specify the following elements:
- The mixing operations to be performed: homogenization, dilution, dissolution…
- The characteristics of the product(s) to be produced, such as density and viscosity.
- Operating conditions like temperature, pressure, or vacuum.
- The projected production volume as well as the target cycle times from clean tank to clean tank.
- You can also include information about the installation site, considering the specific requirements of the location.
- Finally, if you’re handling materials that pose a risk of explosion or flammability, it’s crucial to specify whether ATEX zoning will be necessary to ensure operational safety.
Step 2: Talk to a member of the sales team or a technical expert
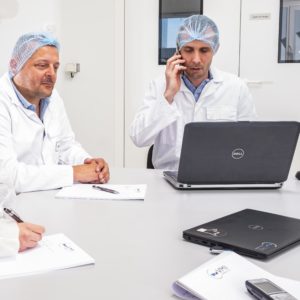
Once your needs are defined, the next step is to identify potential suppliers. Then, reach out to a member of the sales team or a technical expert. Based on the information provided in the specifications, they will guide you toward one or more suitable solutions. They can advise you on the type of tools and equipment required, depending on the specific characteristics of your project. Depending on your process requirements, they may also suggest laboratory tests to ensure that the solutions fully meet your needs.
Step 3: Test the equipment at a testing center or laboratory
Laboratory tests, when possible, are a valuable asset. They allow you to test the process with your ingredients or raw materials and validate the solutions under real conditions. This step offers several advantages:
- Validate the technology: Testing mixers or homogenizers allows you to validate parameters including mixing times and speeds. You can also select the right mixing tool based on the product’s rheology or the nature of the raw materials to be used.
- Testing specific stages: During testing, it is also possible to evaluate specific stages of the process, such as ingredient introduction, mixing, draining, and cleaning—especially for challenging products like mascara—to ensure that each step operates optimally.
- Save time: Trials help you quickly identify your needs using your ingredients and raw materials. They also allow you to anticipate and address any potential technical difficulties before making a purchase.
- Prepare for scale-up: During testing, you can verify that the selected technology is capable of handling complex mixtures and adapting to variable volumes. If you plan to produce at the laboratory or pilot scale before moving to industrial production, testing can help validate your scale up process.
- Compliance: Testing allows you to verify that the solution meets quality and safety standards, reducing the risks of non-compliance.
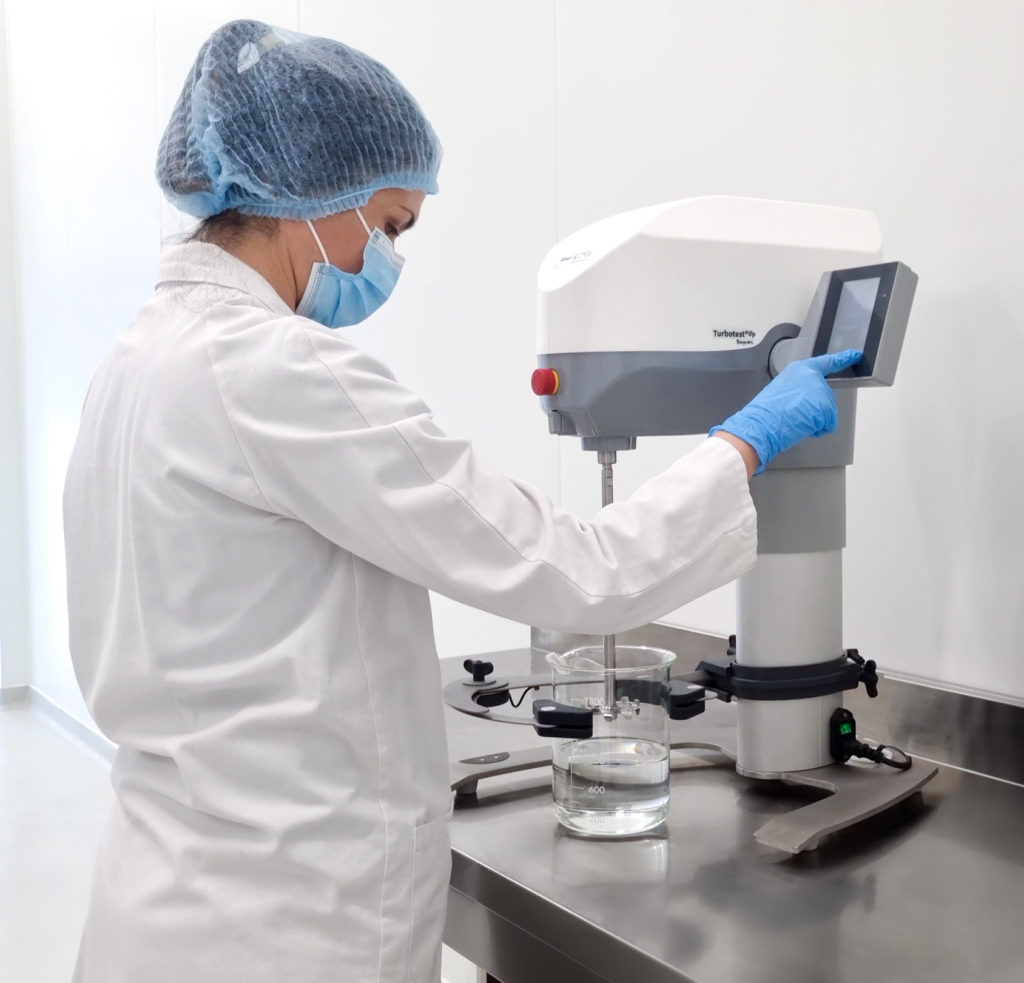
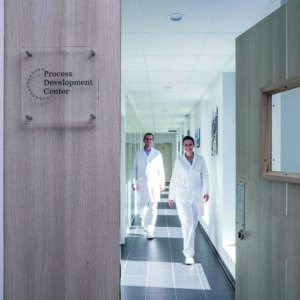
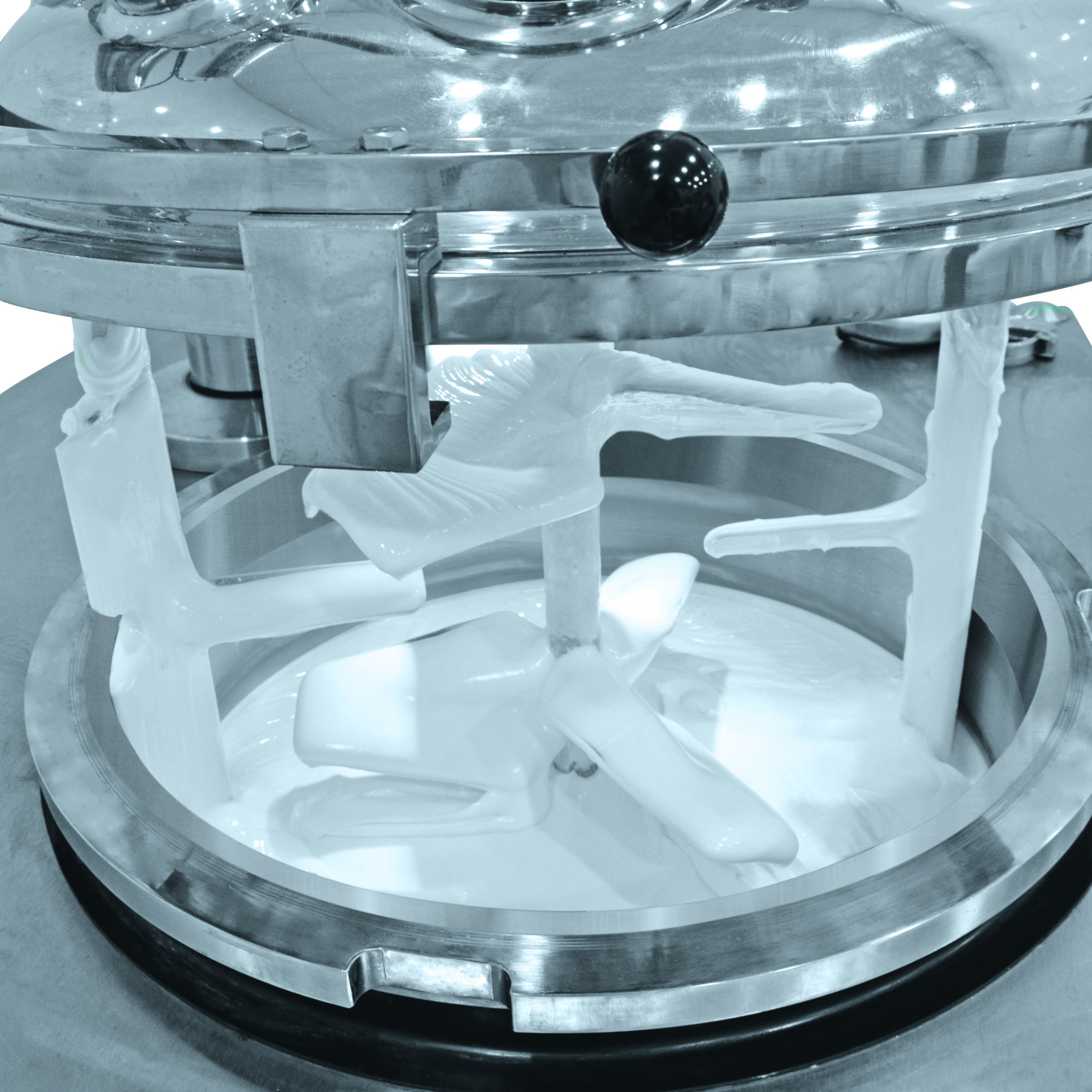
Why choose a manufacturer with a testing center?
Choosing a manufacturer that offers a dedicated testing center is a significant advantage. You can evaluate the equipment’s performance prior to purchase, ensuring it’s perfectly suited to your specific needs.
VMI has a Process Development Center located in France where our clients can test our mixing technologies with personalized technical support. The Process Development Center provides 300 square meters dedicated to testing. It hosts over 20 client tests each year and is equipped with solutions such as the Turbotest® laboratory mixers, the Trilab vacuum pilot homogenizer, the Ultralab® vacuum mixer, and the Trimix vacuum homogenizer.
Since July 2024, VMI also has a testing center in the United States, within the Coperion K-Tron Pitman facilities. The laboratory allows clients to conduct various tests under atmospheric pressure or vacuum. Anne-Marie Kervran, USA-CANADA area manager at VMI, emphasizes the importance of this tech center. She explains: “Clients will have the opportunity to explore vacuum technology, which is becoming mandatory with the MoCRA regulations“. This technology is still underutilized in the United States, but it offers significant advantages for our clients.”
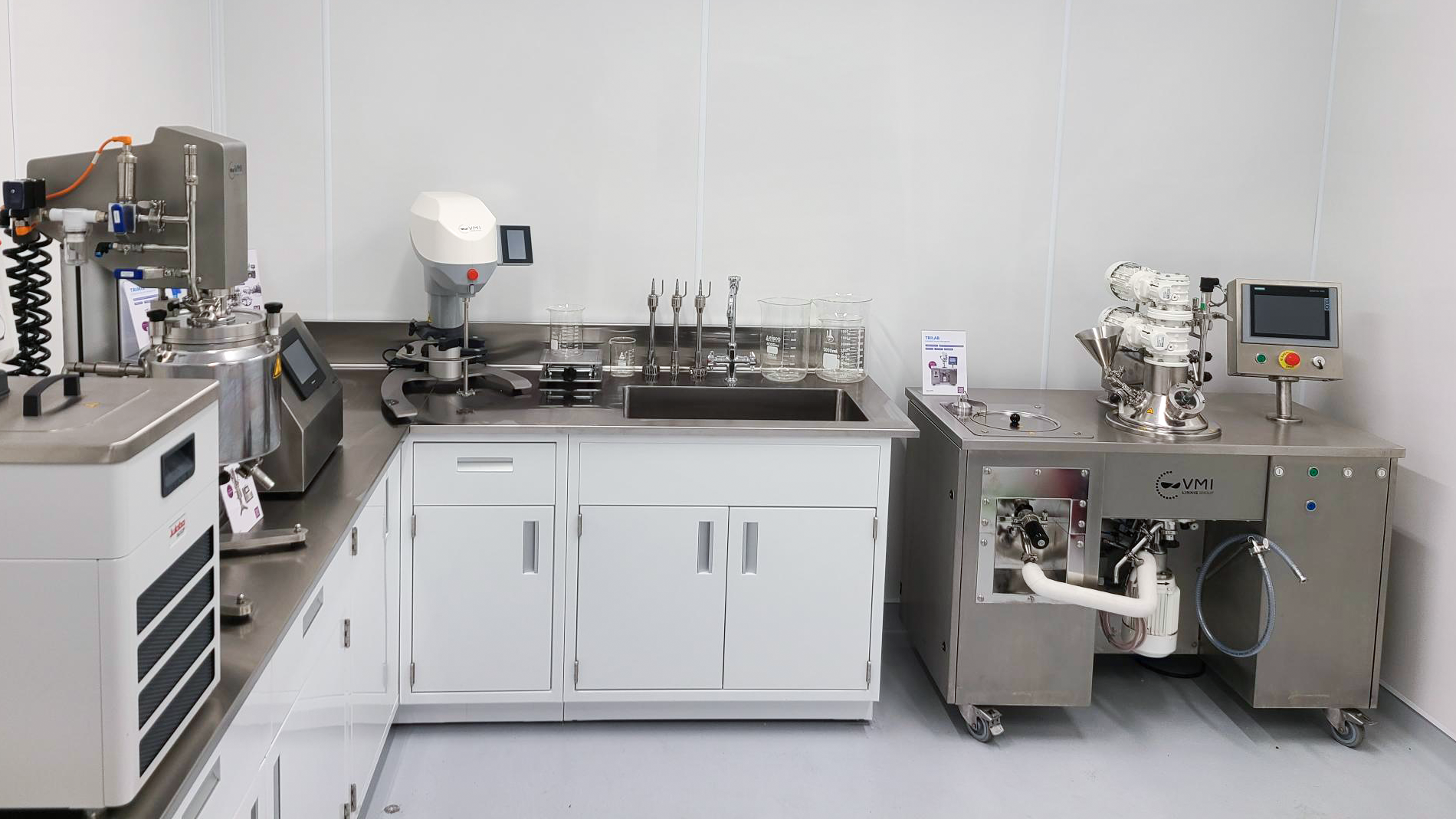
Would you like to come test our equipment?