Manufacturing cosmetic and pharmaceutical products is a complex process that requires a good understanding of the ingredients, technologies and manufacturing processes.
The choice of mixer will strongly impact the efficiency of the process and the final quality of the products. For the cosmetic and pharmaceutical industries, there are several options and technologies available, including vacuum homogenizers.
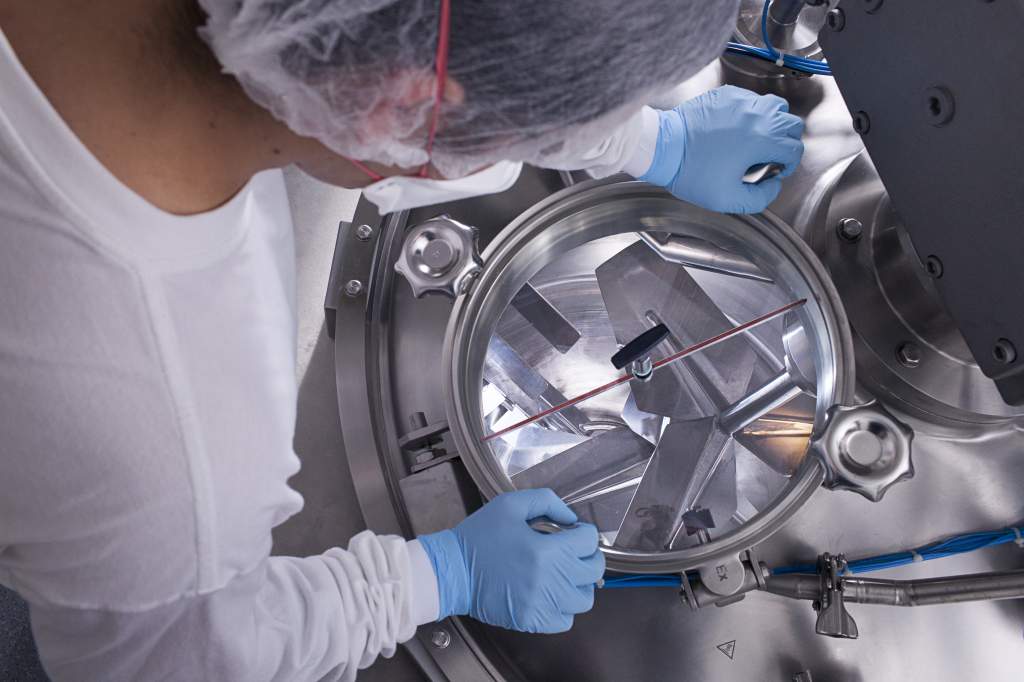
➜ Why choose a vacuum mixer for your production? What are the differences with atmospheric mixers in terms of process?
➜ Which products require vacuum mixing?
Find out in our article.
What is vacuum mixing ?
“Vacuum mixing” means that the mixing process is performed in an environment where the pressure is lower than normal atmospheric pressure. This allows air to be removed from the mixture throughout the process.
The Trimix vacuum homogenizer, for example, can apply vacuum up to 40mbar.
Air bubbles will naturally be added during the mixing operations of a cosmetic product, particularly during the creation of emulsions. The presence of surfactants in the formulation, which is essential for cleansing products and is required for the mixture’s stability, will also encourage the formation of air bubbles.
However, these air bubbles will have unfavorable effects: they will be visible, unsightly, and may prevent the manufacturer from achieving the desired outcome of the final product. In short, the goal in many cases will be to eliminate them.
- A vacuum mixer allows you to apply vacuum throughout the mixing process. Because micro air bubbles are eliminated at the start of the process, there are almost no micro air bubbles at the end.
- An atmospheric mixer, on the other hand, operates at normal atmospheric pressure, which means it does not create vacuum during the mixing process. During the entire mixing process, air is present in the mixer, and a dedicated phase is usually required to naturally evacuate the air bubbles.
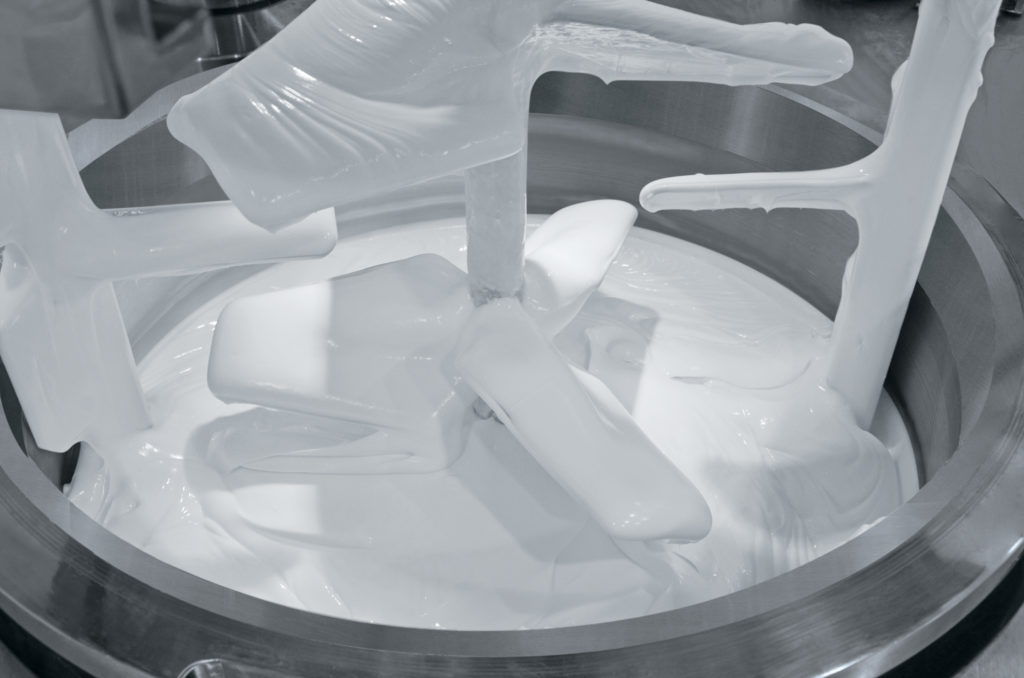
The primary goal of vacuum mixing is to eliminate air bubbles quickly and efficiently throughout the manufacturing process.
Vacuum mixing, for which products ?
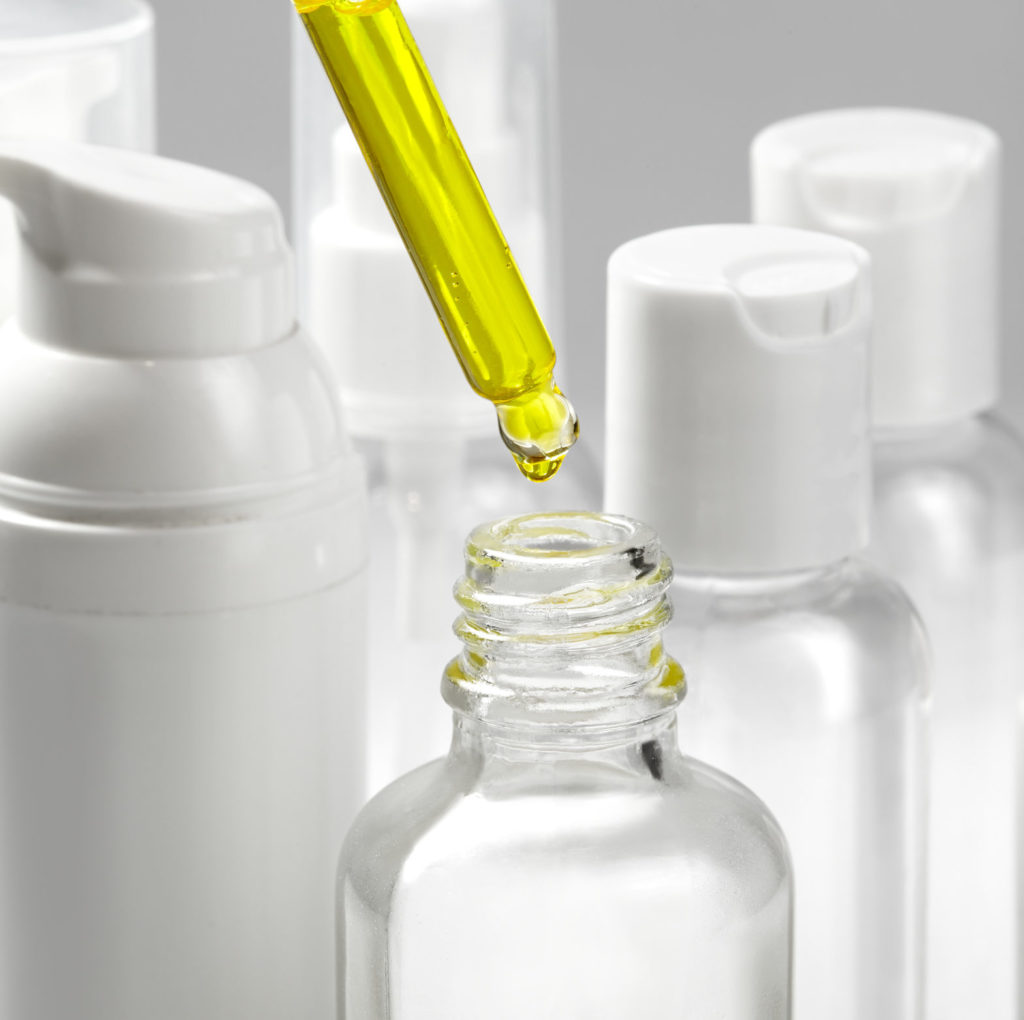
Some products will not require the use of vacuum. This is the case for liquid products such as serums, milks or lotions. As these are very liquid products, the elimination of air bubbles is done easily and naturally throughout the process.
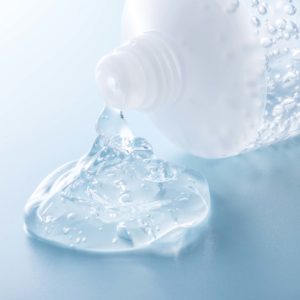
On the other hand, for products with high viscosity such as gels, creams, mascaras or foundations, the natural debubbling phase will be more complex and therefore longer. The air bubbles will have to exert more force to rise to the surface due to the viscosity of the product. For gels, for example, vacuum mixing is strongly recommended because atmospheric mixing will not eliminate all air bubbles, even with an adapted debubbling time.
What are the benefits of vacuum mixing ?
Vacuum mixing has many advantages for cosmetics and pharmaceutical manufacturers.
Product quality and reliability
Vacuum mixing significantly improves the quality and homogeneity of the finished product:
- Visual: The product is more appealing, more brilliant. There are no more bubbles visible to the naked eye. Vacuum mixing allows for translucent products, which is particularly sought after for the production of gels.
- Texture: Due to the elimination of air bubbles, the product is more homogeneous and therefore smooth.
- Application: The product is more fluid, easier to apply and better penetrates the skin.
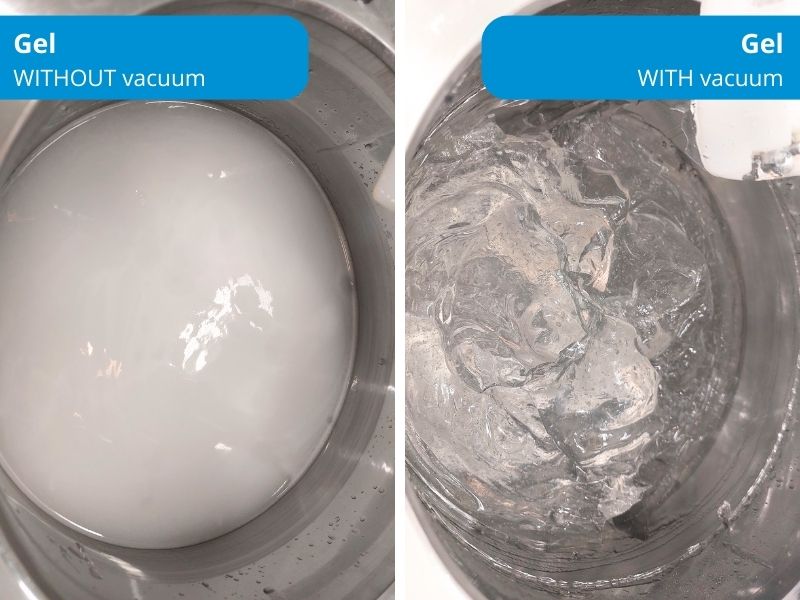
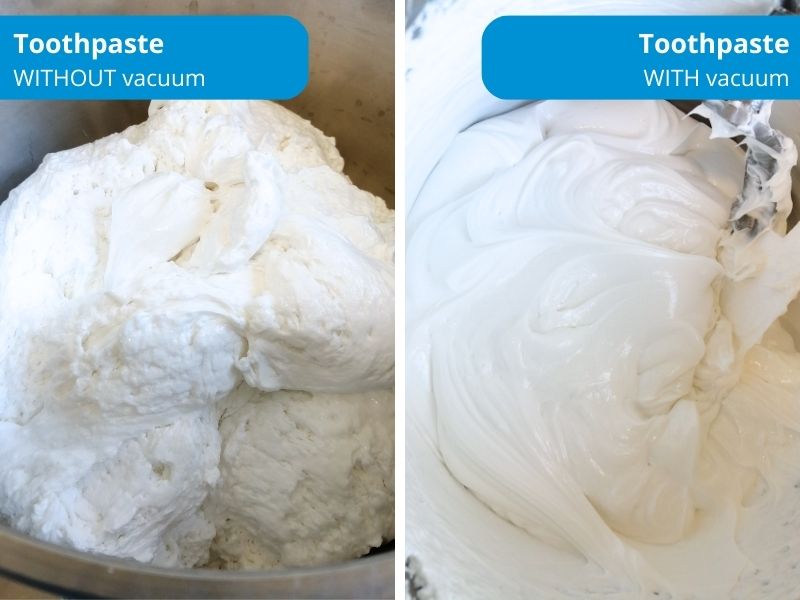
In addition, reducing exposure to air helps prevent product deterioration and bacterial growth due to oxidation. While this risk is negligible in GMP production, vacuum mixing provides additional assurance of the quality and reliability of the finished product.
Process efficiency and productivity
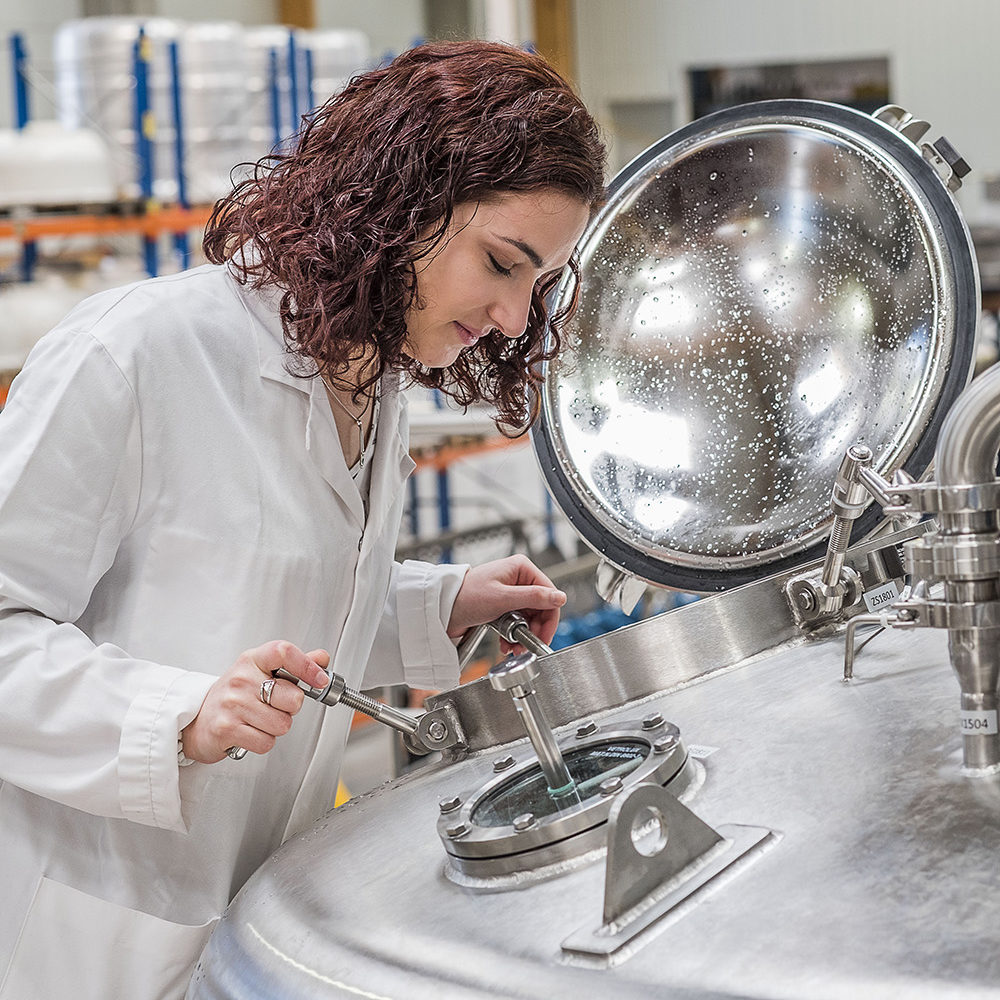
Since the elimination of air bubbles is done throughout the production process, there is no need to plan a dedicated time for debubbling. It is an integrated time that is smoothed out over the entire process. However, there is an exception for products that do not require a heating/cooling phase. It may be necessary to add a vacuum phase since the product cannot finish debubbling during cooling. However, this phase will be much shorter than for natural debubbling.
On the other hand, for an atmospheric mixture, it is necessary to plan a period of natural debubbling which is added to the production time. For a 150L tank, it is generally necessary to count at least 24 hours (this varies depending on the formulation, the process and the type of product).
The mixer is therefore immobilized over this period, which:
- Extends production time
- Delays product packaging
- Prevents the cleaning of the tank
- Blocks the production of a new batch
The impact on productivity is therefore significant. Depending on your usual process, you can significantly reduce your production time by eliminating this particularly time-consuming natural debubbling phase.
Moreover, with a vacuum mixer, you can wash and restart production immediately, without any downtime!
Storage and packaging
The debubbling phase is required not only for the product’s quality but also for its packaging. If air bubbles remain in the containers after filling them, the product will debubble over time. The actual quantity will differ from the one announced. As a result, the batch will be non-compliant. .
To address this issue, some manufacturers add an extra step to their manufacturing process. While waiting for the debubbling, they transfer the product from the mixer to storage tanks. The product is then packaged. This solution increases the mixer’s availability. A dedicated storage space, however, is required, which incurs additional costs.
In conclusion, vacuum mixing is an efficient method for producing high-quality cosmetic and pharmaceutical products. It removes air bubbles much faster than atmospheric mixing, which improves not only the finished product’s quality but also the process’s efficiency and productivity.
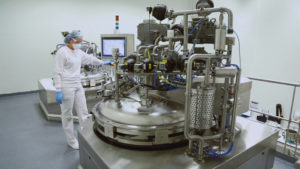
Vacuum mixing is not required for all cosmetic products. However, vacuum homogenizers are versatile pieces of equipment that provide numerous additional benefits. They contribute to the safety and traceability of cosmetic products by allowing for greater control over the ingredients, their introduction, and mixing. It is also easier to drain the product and clean the tank.
Even though a vacuum mixer may require a higher initial investment than an atmospheric mixer, it will quickly pay for itself due to the significant gains in mixing time, machine availability and process efficiency.